Understanding the Art of Welding: Exactly How to Stay Clear Of Undercut Welding Issues for Flawless Fabrication Outcomes
Performance and precision are vital worldwide of welding, where even the least blemish can compromise the structural honesty of a fabricated piece. One usual challenge that welders face is damaging, an issue that can compromise a weld joint and lead to costly rework. By recognizing the origin of undercut welding and carrying out reliable strategies to avoid it, welders can boost their craft to new levels of excellence (Preventing weld undercut). In the quest of remarkable construction outcomes, understanding the art of welding to stay clear of undercut issues is not just an ability yet a necessity for those pursuing perfection in their work.
Understanding Undercut Welding
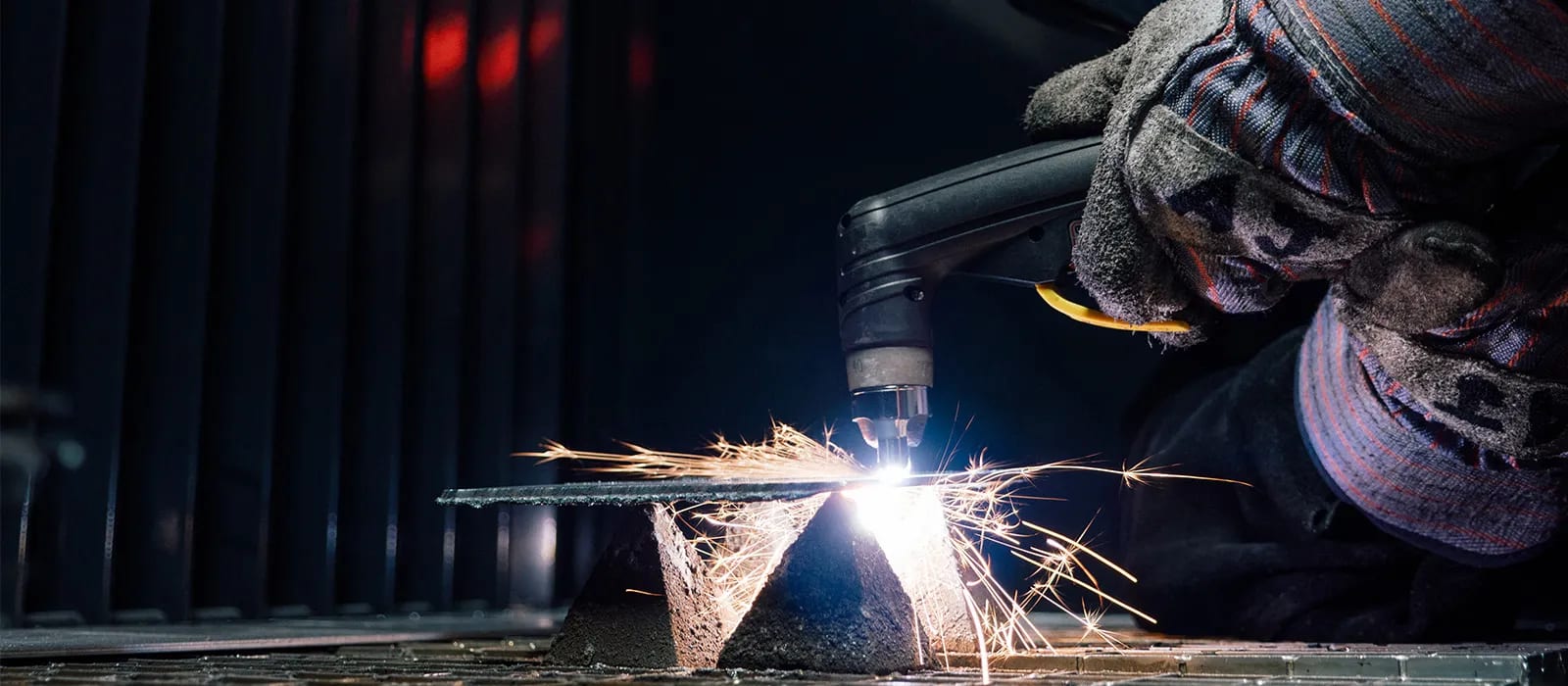
To protect against undercut welding, welders need to ensure correct welding parameters, such as adjusting the current, voltage, travel speed, and maintaining the right electrode angle. By recognizing the reasons of undercut welding and applying preventative actions, welders can attain premium, structurally audio welds.
Root Causes Of Undercut in Welding
Understanding the variables that contribute to damage in welding is necessary for welders to produce top notch, structurally audio welds. Inadequate welding current or wrong welding rate can likewise add to undercut. Comprehending these reasons and implementing appropriate welding strategies can assist protect against undercutting problems, making sure solid and durable welds.
Techniques to Stop Undercutting

To mitigate the risk of damaging in welding, welders can use critical welding strategies intended at boosting the quality and integrity of the weld joints. Additionally, making use of the correct welding strategy for the certain joint setup, such as weave or stringer beads, can contribute to lowering damaging.
In addition, appropriate joint preparation, including ensuring tidy base products without pollutants and using the appropriate welding consumables, is crucial in protecting against undercut defects. Employing try here back-step welding strategies and managing the weld bead account can also aid distribute heat evenly and decrease the danger of undercut. Routine inspection of the weld joint during and after welding, along with executing quality control steps, can help in finding and dealing with undercutting problems without delay. By applying these strategies vigilantly, welders can attain flawless manufacture results with very little undercut defects.
Importance of Correct Welding Parameters
Choosing and keeping appropriate welding parameters is necessary for achieving effective welds with marginal defects. Welding parameters refer to variables such as voltage, present, take a trip speed, electrode angle, and protecting gas circulation price that click to read more straight impact the welding procedure. These criteria must be thoroughly changed based upon the kind of material being welded, its density, and the welding method utilized.
Correct welding criteria make certain the correct amount of heat is put on melt the base metals and filler product evenly. If the criteria are established also high, it can bring about too much warmth input, causing burn-through, distortion, or spatter. On the other hand, if the parameters are too low, insufficient blend, lack of penetration, or undercutting might take place.
Quality Control in Welding Procedures

Final Thought
In final thought, understanding the art of welding needs an extensive understanding of undercut welding, its causes, and strategies to prevent it. By guaranteeing proper welding criteria and carrying out quality guarantee methods, remarkable manufacture results can be achieved. It is necessary for welders to regularly pursue quality in their welding operations to stay clear of undercut issues and generate premium welds.
Undercut welding, a common flaw in welding processes, happens when the weld metal does not properly fill up the groove and leaves a groove or depression along the welded joint.To protect against undercut welding, welders ought to make certain appropriate welding criteria, such as changing the existing, voltage, travel speed, and keeping the right electrode angle. Poor welding wrong or current welding speed can additionally contribute to undercut.To alleviate the risk of damaging in welding, welders can employ strategic welding methods intended at enhancing the high quality and honesty of the weld joints.In conclusion, mastering the art of welding needs an extensive understanding of undercut welding, its reasons, and strategies to prevent it.